Questões de Concurso
Para vestibular
Foram encontradas 1.411 questões
Resolva questões gratuitamente!
Junte-se a mais de 4 milhões de concurseiros!
Qual foi a quantia emprestada?
Estabelece-se como característica necessária:
Qual dos objetivos está incorreto com relação à técnica?
São atividades usuais da Gestão da Qualidade Total:
Dentre essas falhas, destaca-se:
1. O EIA (Estudo de Impacto Ambiental), em geral, constitui-se numa etapa anterior à execução de um projeto. Nessa etapa o estudo tem por função estimar as possíveis implicações de empreendimentos com potencial de degradação ambiental. 2. No Brasil, o EIA ocupou um lugar de destaque somente com a publicação da Lei nº 12.305/2010, que institui a Política Nacional de Resíduos Sólidos (PNRS). 3. O RIMA é o Relatório de Intensões de Melhorias Ambientais e faz parte do Plano de monitoramento que deve ser feito após o EIA.
Assinale a alternativa que indica todas as afirmativas corretas.
Qual elemento abaixo não faz parte desses subsistemas?
1. Global Reporting Initiative, Ceres Reporting e balanço social segundo o Ibase são ou foram tipos de relatórios ambientais que podem ser utilizados pelas empresas para comunicar sua responsabilidade social. 2. Segundo o Prof. Barbieri, conforme cita o livro da Academia Pearson sobre Gestão Ambiental, existem 3 princípios que estabelecem a responsabilidade socioambiental: o princípio da legitimidade, o da responsabilidade pública e o princípio do agente moral, contribuindo para a ação responsável e ética. 3. O instituto Ethos foi criado em 1998. Trata-se de uma organização sem fins lucrativos que criou uma série de indicadores que avaliam a atuação das organizações no tocante à sua responsabilidade socioambiental.
Assinale a alternativa que indica todas as afirmativas corretas.
Das técnicas abaixo, assinale a incorreta.
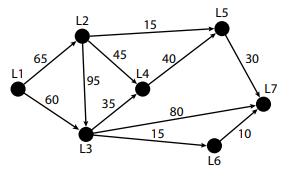
É correto afirmar que a quantidade máxima de materiais, em kg, que a empresa pode transportar é igual a:
Responda à questão a partir do enunciado a seguir.
Considere o seguinte problema de programação linear (P) com duas variáveis de decisão, x1 e x2.
(P) max
3x1 + 2x2
4x1 - x2 ≤ 8
4x1 - 3x2 ≤ 12
4x1 + x2 ≤ 8
x1,x2 ≥ 0
É correto afirmar nesse caso que o preço dual dessa restrição é igual a:
Responda à questão a partir do enunciado a seguir.
Considere o seguinte problema de programação linear (P) com duas variáveis de decisão, x1 e x2.
(P) max
3x1 + 2x2
4x1 - x2 ≤ 8
4x1 - 3x2 ≤ 12
4x1 + x2 ≤ 8
x1,x2 ≥ 0
Tabela 1 Disponibilidade e preço dos insumos Tipos de Insumos Quantidade Máxima Disponível (kg/dia) Custo por kg/dia (R$) 1 2000 23 2 1350 16 3 1750 15 4 950 29
Tabela 2 Percentuais mínimos e máximos de cada insumo em cada produto Tipos de Produto Especificação Preço de Venda R$/kg
• Não mais que 35% do insumo 1
P1 • Não menos que 20% do insumo 2 28
• Não mais que 70% do insumo 3
• Não mais que 40% do insumo 1 P2 50 • Não menos que 18% do insumo 2 P3 • Não mais que 75% do insumo 1 40Observe a especificação do produto P2 em relação ao insumo 1: “Não mais que 40% do insumo 1”. Esta especificação gera uma restrição significando que, mesmo o produto P2 sendo formado por uma mistura dos insumos 1, 2, 3 e 4, o total de insumo 1 presente na mistura deve ser menor ou igual a 40% do total de todos os insumos.
Considerando as variáveis de decisão xij como as quantidades de insumo j utilizadas para a produção do produto i, pode-se afirmar que a restrição de especificação do produto P2, “Não mais que 40% do insumo 1”, conforme mostra a Tabela 2, pode ser expressa matematicamente por:
A Brief and Simplified Description of Papermaking
The paper we use today is created from individual wood fibers that are first suspended in water and then pressed and dried into sheets. The process of converting the wood to a suspension of wood fibers in water is known as pulp making, while the manufacture of the dried and pressed sheets of paper is formally termed papermaking. The process of making paper has undergone a steady evolution, and larger and more sophisticated equipment and better technology continue to improve it.
The Wood yard and Wood rooms
The process at Androscogging began with receiving wood in the form of chips or of logs 4 or 8 feet in length. From 6 AM to 10 PM a steady stream of trucks and railroad cars were weighted and unloaded. About 40 percent were suplied by independents who were paid by weight their logs. The mill also received wood chips from lumber mills in the area. The chips and logs were stored in mammoth piles with separate piles for wood of different species (such as pine, spruce, hemlock).
When needed, logs were floated in flumes......(1).....the wood yard.....(2).....one of the mill’s three wood rooms. There, bark was rubbed......(3)........in long, ribbed debarking drums by tumbling the logs against one another. The logs then fell into a chipper;......(4)......seconds a large log was reduced to a pile of chips approximately 1 inch by 1 inch by 1/4 inch.
The chips were stored in silos. There were separate silos for softwoods (spruce, fir, hemlock, and pine) and hardwoods (maple, oak, beech, and birch). This separate and temporary storage of chips permitted the controlled mixing of chips into the precise recipe for the grade of paper being produced.
The wood chips were then sorted through large, flat vibrating screens. Oversized chips were rechipped, and ones that were too small were collected for burning in the power house. (The mill provided approximately 20 percent of all its own steam and electricity needs from burning waste. An additional 50 percent of total electricity needs was produced by harnessing the river for hydroelectric power.)
Once drawn from the silo into the digesters, there was no stopping the flow of chips into paper.
Pulpmaking
The pulp made at Androscoggin was of two types: Kraft pulp (produced chemically) and ground wood pulp (produced mechanically). Kraft pulp was far more important to the high quality white papers produced at Androscoggin, accounting for 80 percent of all the pulp used. Kraft pulp makes strong paper. (Kraft is German for strength. A German invented the Kraft pulp process in 1884.) A paper’s strength generally comes from the overlap and binding of long fibers of softwood; only chemically was it initially possible to separate long wood fibers for suspension in water. Hardwood fibers are generally smaller and thinner and help smooth the paper and make it less porous.
The ground wood pulping process was simpler and less expensive than the Kraft process. It took high quality spruce and fir logs and pressed them continuously against a revolving stone that broke apart the wood’s fibers. The fibers, however, were smaller than those produced by the Kraft process and, although used to make newsprint, were useful at Androscoggin in providing “fill” for the coated publication gloss papers of machines 2 and 3, as will be described later.
(A)The chemical Kraft process worked by dissolving the lignin that bonds wood fibers together. (B) It did this in a tall pressure cooker, called a digester, by “cooking” the chips in a solution of caustic soda (NaOH) and sodium sulfide (Na2S), which was termed the “white liquor.” (C)The two digesters at Androscoggin were continuous digesters; chips and liquor went into the top, were cooked together as they slowly settled down to the bottom, and were drawn off the bottom after about three hours. (D) By this time, the white liquor had changed chemically to “black liquor’’; the digested chips were then separated from this black liquor. (E)
In what was known as the “cold blow” process, the hot, pressurized chips were gradually cooled and depressurized. A “cold liquor’’ (170°F) was introduced to the bottom of the digester and served both to cool and to transport the digested chips to a diffusion washer that washed and depressurized the chips. Because so much of the lignin bonding the fibers together had been removed, the wood fiber in the chips literally fell apart at this stage.
The black liquor from the digester entered a separate four-step recovery process. Over 95 percent of the black liquor could be reconstituted as white liquor, thereby saving on chemical costs and significantly lowering pollution. The four-step process involved (1) washing the black liquor from the cooked fiber to produce weak black liquor, (2) evaporating the weak black liquor to a thicker consistency, (3) combustion of this heavy black liquor with sodium sulfate (Na2SO4 ), and redissolving the smelt, yielding a “green liquor” (sodium carbonate + sodium sulfide), and (4) adding lime, which reacted with the green liquor to produce white liquor. The last step was known as causticization.
Meanwhile, the wood-fiber pulp was purged of impurities like bark and dirt by mechanical screening and by spinning the mixture in centrifugal cleaners. The pulp was then concentrated by removing water from it so that it could be stored and bleached more economically.
By this time, depending on the type of pulp being made, it had been between 3 1/2 and 5 hours since the chips had entered the pulp mill.
All the Kraft pulp was then bleached. Bleaching took between 5 and 6 hours. It consisted of a three-step process in which (1) a mix of chlorine (Cl2 ) and chlorine dioxide (CIO2 ) was introduced to the pulp and the pulp was washed; (2) a patented mix of sodium hydroxide (NaOH), liquid oxygen, and hydrogen peroxide (H2 O2 ) was then added to the pulp and the pulp was again washed; and (3) chlorine dioxide (ClO2 ) was introduced and the pulp washed a final time. The result was like fluffy cream of wheat. By this time the pulp was nearly ready to be made into paper.
From the bleachery, the stock of pulp was held for a short time in storage (a maximum of 16 hours) and then proceeded through a series of blending operations that permitted a string of additives (for example, filler clay, resins, brighteners, alum, dyes) to be mixed into the pulp according to the recipe for the paper grade being produced. Here, too, “broke” (paper wastes from the mill itself) was recycled into the pulp. The pulp was then once again cleaned and blended into an even consistency before moving to the papermaking machine itself.
It made a difference whether the broke was of coated
or uncoated paper, and whether it was white or colored. White, uncoated paper could be recycled immediately. Colored, uncoated paper had to be rebleached.
Coated papers, because of the clays in them, could not
be reclaimed.
The underlined is closest to the meaning to: