Questões de Concurso
Para vestibular
Foram encontradas 1.411 questões
Resolva questões gratuitamente!
Junte-se a mais de 4 milhões de concurseiros!
Analise as afirmativas abaixo sobre as três funções centrais que qualquer organização apresenta.
1. Em uma empresa de Caridade, a função de desenvolvimento de produto ou serviço é responsável por desenvolver novas campanhas de solicitação de recursos e projetar novos programas de assistência.
2. Em uma empresa provedora de serviços de internet, a função de manutenção é responsável por manter equipamentos e as informações disponibilizadas aos clientes.
3. Em uma cadeia de fast-food, a função de marketing é responsável por desenvolver o material promocional e realizar a divulgação do mesmo nos meios de comunicação utilizados pela empresa.
Assinale a alternativa que indica todas as afirmativas corretas.
Os centros de produção da empresa são tais que se toda a produção for dedicada à produção de capas para iPod, 6000 capas podem ser produzidas em um dia. Se toda a produção for dedicada para capas de iPhone ou iPad, 5000 ou 3000 delas podem ser produzidas em um dia.
O planejamento da produção é de uma semana (5 dias úteis), e a produção semanal deve ser estocada antes da distribuição. O estoque de 1000 capas de iPod ocupa até 40 pés cúbicos de espaço. O estoque de 1000 capas de iPhone ocupa até 45 pés cúbicos de espaço, e estocar 1000 capas de iPad ocupa até 210 pés cúbicos. O espaço total de estoque disponível é de 6000 pés cúbicos.
Devido a acordos comerciais com a Apple, a empresa Acessórios e Cia tem que entregar no mínimo 5000 capas de iPod e 4000 capas de iPad por semana. O departamento de marketing estima que a demanda semanal por capas de iPod, iPhone e iPad não excede 10000, 15000 e 8000 unidades, respectivamente. Portanto, a empresa não quer produzir mais que essas quantidades de capas para iPod, iPhone e iPad.
Finalmente, o lucro líquido por cada capa de iPod, capa de iPhone e capa de iPad é R$ 4,00, R$ 6,00 e R$ 10, respectivamente. O objetivo é determinar a produção semanal que maximiza o lucro total líquido.
A restrição de estoque máximo do problema é dada por:
O custo de transporte entre as fábricas e os centros consumidores são apresentados na tabela abaixo:
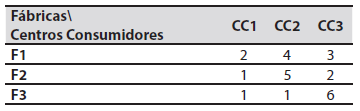
Aplicando-se o método do Custo Mínimo, que consiste em transportar o máximo possível entre as rotas mais baratas, obtém-se uma solução inicial, que não necessariamente é a solução ótima para o problema, com custo igual a:
Considere o seguinte problema de programação linear abaixo com 3 variáveis e 2 restrições:
É correto afirmar que o valor da função objetivo no ponto ótimo é igual a:
Considerando que, em um certo ano, a inflação tenha sido 4%, qual foi o rendimento da aplicação de João?
Quais foram os custos de transformação unitários (R$/un) de P1 e P2 em março?
1. Os custos fixos não são afetados por variações no volume de produção, no curto prazo.
2. Os custos variáveis sempre acompanham a variação no volume de produção de forma linear.
3. Os custos fixos unitários alteram-se em função de variações no volume de produção.
4. Um custo fixo é o que apresenta o mesmo valor durante vários meses.
5. A classificação entre custos fixos e variáveis é utilizada principalmente para auxílio ao controle.
Assinale a alternativa que indica todas as afirmativas corretas.
Analise as afirmativas abaixo sobre esses instrumentos de avaliação:
1. O EIA, em geral, constitui-se numa etapa anterior à execução de um projeto. Nessa etapa o estudo tem por função estimar as possíveis implicações de empreendimentos com potencial de degradação ambiental.
2. Três são as etapas de análise do EIA, segundo a Resolução CONAMA: i) impactos ambientais nas fases de implantação e operação, ii) limites da área geográfica atingida pelo projeto, e iii) planos e programas de mitigação dos impactos.
3. O RIMA é o Relatório de Intensões de Melhorias Ambientais e faz parte do Plano de Monitoramento que deve ser feito após o EIA.
Assinale a alternativa que indica todas as afirmativas corretas.
Analise as afirmativas abaixo com relação ao conceito de logística reversa:
1. São exemplos de avanços em legislações de diversos países, com relação à logística reversa: ISO 9001, RoHS – Restrictions for Hazardous Substances e WEEE – Waste from Electrical and Electronic Equipment.
2. Há duas categorias de canais de distribuição reversos: i) os canais de distribuição reversos de pós-consumo e ii) os canais de distribuição reversos de pós-venda.
3. Os canais reversos de pós-consumo são constituídos pelas diferentes formas e possibilidades de retorno de uma parcela de produtos, com pouco ou nenhum uso, motivados por problemas relacionados à qualidade em geral ou processos comerciais entre empresas, retornando o ciclo de negócios de alguma maneira.
Assinale a alternativa que indica todas as afirmativas corretas.
Qual das alternativas apresentadas abaixo está incorreta?
Qual das recomendações está incorreta com respeito à sua técnica?
1. Análise da demanda.
2. Análise do layout.
3. Análise do processo.
4. Análise da tarefa.
5. Análise da atividade.
Assinale a alternativa que indica todas as afirmativas corretas
1. Características gerais: sexo, idade, etnia, origem.
2. Instrução e experiências: nível de instrução, conhecimentos específicos, experiências especiais.
3. Características físicas: dimensões corporais, características psicomotoras, características sensoriais.
4. Características psicossociais: inteligência geral, habilidades, personalidade.
Assinale a alternativa que indica todas as afirmativas corretas.
Assinale a alternativa incorreta.